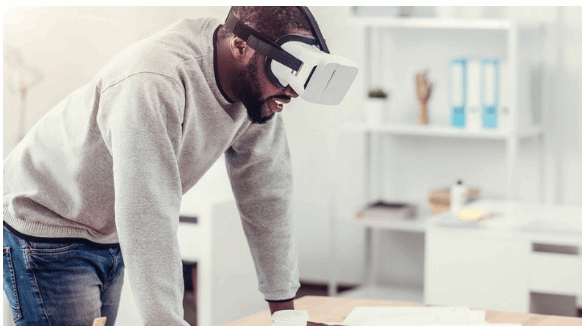
At a time when oil and gas companies are paying particularly close attention to improving efficiencies and cost-cutting, they would do well to increase their usage of 3D scanning technology, according to the engineering firm Kleinfelder.
The company contends that 3D scanning enables engineers to remotely plan upgrades to oil and gas assets in a virtual setting using models. Although the original scan needs to be performed physically by an engineer using a specialized 3D camera that can reveal hidden pipe systems and other elements behind walls or underground, most of the work can be done remotely on computers or other shared devices, it explained in a written statement.
Mark Franklin, 3D Reality Capture Lead Account Manager with Kleinfelder, told Rigzone that laser scanning devices capture millions of data points to measure an object or space using laser infrared technology, producing detailed 3D images in a minutes. The images consist of millions of 3D data points, which are known as a “point cloud,” he said.
“The laser scanner emits a beam of infrared laser light onto a rotating mirror that spins and effectively paints the surrounding environment with light,” Franklin explained. “As the scanner rotates the objects in the path of the laser reflect the beam back to the scanner, providing the geometry that is interpreted into 3D data. In addition to the distance measurement, laser scanners also capture measurements on the horizontal and vertical planes, providing a full scope of measurement data.”
Franklin observed that asset owners need to have confidence in existing conditions and limit costly assumptions before taking on an infrastructure upgrade.
“3D scanning solutions provide clients with highly detailed and reality-rich 3D data that streamlines the design and construction process – reducing project risk,” he said.
Franklin also pointed out that 3D scanning offers oil and gas industry players the opportunity to refine existing processes, yielding safety, construction and maintenance cost benefits and helping to lower the environmental footprint of their assets.
“Having the ability to have highly accurate model information that is accessible through online applications assists with all those aspects and, therefore, we are seeing a lot of support for these new technologies as companies look at any way to improve efficiencies,” he explained.
A partial list of current oil and gas industry 3D scanning applications includes:
- Mission-critical facilities piping and equipment replacement projects
- Safety and equipment reliability-driven degradation and corrosion assessments (such as tank wall assessment and fireproofing)
- Enhanced engineering assessment of large-diameter overhead piping and other complex and inaccessible equipment
- Virtual reality for process operator immersion and emergency response training, along with constructability visualization
- Full-color 3D viewing access to site data without going to the site, including access to a web portal of all projects for virtual inspections
- Ability to conduct a full site walk-throughs for project scoping, volume calc reports, bidding or planning purposes
- Project planning in color 3D high-resolution from a planner’s desk, requiring no site access.
“As for the future, we are starting to work on some exciting projects where we have teamed up with a machine learning company to explore using the captured data for different types of projects such as inspection analysis,” said Franklin. “With all this captured data that we collect, it becomes very valuable to figure out new ways to use this and machine learning and artificial intelligence is something we are excited to explore.”
Franklin also noted that some emerging uses for 3D scanning include:
- Capturing and analyzing site conditions
- Identifying peripheral asset clashes
- Performing 3D modeling and design
- Measuring piping, steel and infrastructure elements
- Turnaround support and planning.
Applying 3D scanning also provides a pathway for oil and gas companies to integrate various technological concepts such as the Internet of Things (IoT), digital twins, machine learning, artificial intelligence, augmented reality and mixed reality, added Franklin.
“3D scanning is often the first step that can be used when exploring any of these technologies since it is giving us the ability to capture the real-life virtual model of the existing asset,” he said. “We then utilize that as the basis for creating digital twin models of facilities that can also be tied into existing and live asset management systems.”
A virtual live “breathing” model of the existing facility begins to materialize once the systems are linked to IoT hardware and software, continued Franklin.
“Since there is so much to chase in this field, and there are limited funds, we think it is a matter of taking baby steps and small bits when looking into these solutions with our clients,” he added. “Technology is advancing fast in these areas, which is making it much more cost-effective to explore these options than it was even a few years ago.”
To contact the author, email mveazey@rigzone.com.
No comments:
Post a Comment